News
Unveiling the Secrets of Carbide Coolant Drills: A Deep Dive into Technology
Release time:
2025/07/07
Unveiling the Secrets of Carbide Coolant Drills: A Deep Dive into Technology
In the world of industrial machining, precision and efficiency are paramount. As manufacturers seek out advanced solutions to improve productivity, carbide coolant drills have emerged as a game-changing innovation. This article aims to explore the intricate technology behind these drills, examining their construction, benefits, applications, and maintenance practices. By the end, you’ll have a comprehensive understanding of carbide coolant drills and how they can elevate your operational capabilities.
Table of Contents
- What Are Carbide Coolant Drills?
- The Technology Behind Carbide Drills
- Advantages of Using Carbide Coolant Drills
- Applications of Carbide Coolant Drills
- Maintenance Tips for Carbide Drills
- Selecting the Right Carbide Drill for Your Needs
- Common Misconceptions About Carbide Drills
- The Future of Carbide Drill Technology
- Conclusion
- Frequently Asked Questions (FAQs)
What Are Carbide Coolant Drills?
Carbide coolant drills are specialized drilling tools designed for high-performance machining applications. Made from a tungsten carbide alloy, these drills incorporate channels for coolant delivery, allowing for effective temperature management during drilling processes. This innovative design enhances tool life and maintains precision in various materials, from metals to composites.
Understanding the Composition of Carbide
Tungsten carbide is a composite material formed by the combination of tungsten and carbon. This material is known for its exceptional hardness and wear resistance, making it ideal for cutting tools. The incorporation of coolant channels significantly improves the drill's efficiency, making it a preferred choice in high-speed machining environments.
The Technology Behind Carbide Drills
The technology that drives carbide coolant drills is a culmination of advanced engineering and material science. The precise geometry of the drill bits, combined with the innovative coolant delivery systems, results in superior performance. Let's delve deeper into the technical aspects that set these drills apart.
Coolant Delivery Systems
One of the standout features of carbide coolant drills is their integrated coolant delivery systems. These systems ensure that coolant reaches the cutting edge, effectively dissipating heat generated during the drilling process. By maintaining optimal temperatures, these drills prevent overheating, which can lead to tool wear or failure.
Geometric Design and Performance
The geometric design of carbide coolant drills plays a critical role in their effectiveness. The angles and flutes are strategically designed to enhance chip removal and minimize friction. This not only improves drilling efficiency but also contributes to a smoother finish on the workpiece.
Advantages of Using Carbide Coolant Drills
Carbide coolant drills offer numerous advantages that make them indispensable in modern machining. Understanding these benefits can help businesses make informed decisions about their tooling options.
Enhanced Tool Life
One of the primary benefits of using carbide coolant drills is their extended tool life. The combination of heat management and wear resistance allows these drills to maintain their cutting edges for longer periods, reducing the frequency of replacements.
Improved Precision
Precision is critical in machining, and carbide coolant drills excel in this area. The controlled temperature and optimized design facilitate accurate drilling, ensuring that the dimensions of the workpiece meet stringent specifications.
Increased Productivity
With their ability to tackle high-speed drilling operations, carbide coolant drills significantly boost productivity. The effective chip removal and reduced friction enable faster feed rates, allowing for more parts to be produced in less time.
Applications of Carbide Coolant Drills
Carbide coolant drills find applications across various industries due to their versatility and efficiency. Here are some common sectors where these drills are utilized.
Aerospace Industry
The aerospace sector demands high precision and reliability. Carbide coolant drills are often used for drilling aircraft components, where the integrity of each hole is crucial for safety and performance.
Automotive Manufacturing
In automotive manufacturing, carbide drills are employed to create precise holes in engine blocks, transmissions, and other critical components. Their durability and efficiency make them ideal for high-volume production runs.
Medical Device Manufacturing
The medical device industry requires strict adherence to quality standards. Carbide coolant drills are used to produce intricate holes in devices such as surgical instruments and implants, ensuring accuracy and reliability.
Maintenance Tips for Carbide Drills
Proper maintenance of carbide coolant drills is essential for maximizing their performance and lifespan. Here are some key maintenance practices to consider.
Regular Inspection
Routine inspections can help identify wear and damage early. Look for signs of chipping or blunt edges, as these can significantly impact drilling efficiency.
Cleaning and Lubrication
After use, thoroughly clean the drills to remove any debris or coolant residues. Additionally, applying a suitable lubricant can help prevent corrosion and maintain optimal performance.
Sharpening Techniques
Sharpening carbide drills requires specialized tools and techniques. It’s crucial to follow manufacturer guidelines to ensure that the geometry is preserved, which is vital for the drill’s performance.
Selecting the Right Carbide Drill for Your Needs
Choosing the right carbide drill involves considering several factors, including material type, hole diameter, and drilling depth. Here’s a breakdown of what to look for when selecting a drill.
Material Compatibility
Evaluate the materials you will be drilling. Different carbide drill designs cater to specific materials, so selecting one that matches your application's requirements is essential for optimal results.
Drill Diameter and Length
Choose a drill with the appropriate diameter and length for your project. The right specifications ensure that you achieve the desired hole size without compromising efficiency.
Common Misconceptions About Carbide Drills
Despite their advantages, several misconceptions surround carbide coolant drills. Understanding these can help users make better-informed decisions.
Myth: Carbide Drills Are Only for Metal
While carbide drills excel in metalworking, they are also effective in drilling composite materials, plastics, and other substrates. Their versatility makes them suitable for a wide range of applications.
Myth: Higher Cost Means Better Quality
While carbide drills can be more expensive than traditional options, it’s essential to evaluate their performance and longevity rather than solely focusing on upfront costs. In many cases, the investment pays off through increased productivity and reduced tool wear.
The Future of Carbide Drill Technology
As technology continues to advance, the future of carbide drill technology looks promising. Innovations in materials, coatings, and designs are likely to enhance performance even further. Trends toward automation and smart tooling systems will also influence how carbide drills are manufactured and utilized in various industries.
Conclusion
Carbide coolant drills represent a significant advancement in machining technology, offering exceptional performance, durability, and versatility. Their ability to maintain precision while managing heat makes them an invaluable asset in various industries. By understanding their technology, applications, and maintenance, businesses can leverage carbide coolant drills to enhance their productivity and efficiency in machining processes. Embracing this technology will ensure you stay ahead in today’s competitive industrial landscape.
Frequently Asked Questions (FAQs)
1. What is the primary material used in carbide coolant drills?
The primary material is tungsten carbide, known for its exceptional hardness and wear resistance, making it ideal for cutting tools.
2. How do coolant channels benefit carbide drills?
Coolant channels deliver coolant directly to the cutting edge, reducing heat buildup and prolonging tool life while improving drilling efficiency.
3. Can carbide drills be reused after sharpening?
Yes, carbide drills can be sharpened and reused, but it's essential to follow proper techniques to maintain their geometry and performance.
4. Are carbide drills suitable for drilling plastic materials?
Yes, carbide drills are versatile and can effectively drill plastic, composites, and various metal types, making them suitable for diverse applications.
5. What factors should be considered when selecting a carbide drill?
Consider material compatibility, required hole diameter, drilling depth, and specific application requirements when selecting the appropriate carbide drill.
keywords
Latest News
Contact Information
Tel: +86-18861298766
E-mail: jeni@vellfire-tools.com
Whatsapp:8618861298766
Address: No. 156, Nanxi Road, Xinbei District, Changzhou City (Wilfa Recutting Milling Cutter and High Efficiency Drill Wholesale)

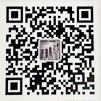

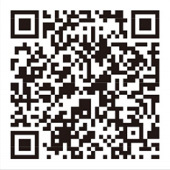
Copyright© 2023 Jiangsu Vellfire Precision Alloy Co., Ltd. All Rights Reserved