News
Enhancing Productivity with Advanced End Mill Solutions for Mould Steel Processing
Release time:
2025/07/21
Enhancing Productivity with Advanced End Mill Solutions for Mould Steel Processing
Table of Contents
- Introduction to Mould Steel Processing
- Understanding End Mills: The Backbone of Precision Machining
- Choosing the Right End Mill for Mould Steel Processing
- Cutting Parameters and Their Impact on Productivity
- Advanced Coating Technologies for Enhanced Tool Life
- Current Trends in End Milling Techniques
- Measuring Productivity Gains with End Mill Solutions
- Frequently Asked Questions
- Conclusion: The Future of End Mill Solutions in Mould Steel Processing
Introduction to Mould Steel Processing
The manufacturing industry heavily relies on **mould steel processing** to produce high-quality components used in various applications, from automotive parts to consumer electronics. In this highly competitive environment, enhancing productivity while ensuring precision and quality is paramount. The selection of the right tools, particularly **end mills**, plays a crucial role in achieving these goals. This article explores innovative end mill solutions tailored for mould steel processing, providing insights into cutting-edge technologies, advanced machining techniques, and best practices.
Understanding End Mills: The Backbone of Precision Machining
End mills are pivotal in various machining operations, especially in mould steel processing. Unlike drill bits, end mills can cut in all directions, making them ideal for creating complex shapes and features in metal. They come in various sizes, geometries, and materials, allowing for versatility in milling operations.
**Key Features of End Mills:**
- **Flute Design:** The number of flutes affects chip removal and cutting speed. More flutes increase surface finish but may reduce chip clearance.
- **Coating:** Different coatings enhance tool performance and durability, allowing for higher speeds and feeds.
- **Geometry:** The shape of the cutting edge influences how the tool interacts with the material, affecting cutting forces and tool life.
Understanding these features is essential for selecting the right end mill to meet specific production requirements.
Choosing the Right End Mill for Mould Steel Processing
Selecting the appropriate end mill for mould steel processing requires careful consideration of several factors. The type of steel, desired surface finish, and specific machining conditions all influence tool choice.
Types of End Mills for Mould Steel
1. **Carbide End Mills:** Renowned for their hardness and wear resistance, carbide end mills are ideal for machining tough mould steels. They maintain sharp cutting edges and withstand high temperatures.
2. **High-Speed Steel (HSS) End Mills:** While less durable than carbide, HSS end mills are cost-effective and suitable for softer materials or less demanding applications.
3. **Coated End Mills:** Various coatings, such as TiN, TiAlN, and PVD, enhance the performance of end mills, providing improved wear resistance and reducing friction.
Considerations for Tool Selection
- **Material Compatibility:** Match the end mill material with the mould steel type to optimize performance and tool life.
- **Geometry and Flute Count:** Select the appropriate geometry and number of flutes based on the desired surface finish and machining strategy.
- **Cutting Conditions:** Assess the cutting speed, feed rate, and depth of cut to ensure efficient material removal without compromising tool integrity.
Cutting Parameters and Their Impact on Productivity
Optimizing cutting parameters is crucial for enhancing productivity in mould steel processing. The following factors significantly influence machining efficiency:
Cutting Speed
The cutting speed, or surface speed, refers to how fast the end mill revolves while cutting. Higher cutting speeds can increase productivity but may also generate more heat, leading to tool wear. Finding the optimal cutting speed is essential for balancing productivity and tool longevity.
Feed Rate
The feed rate is the speed at which the workpiece moves into the cutting tool. A higher feed rate can boost productivity but may compromise surface finish and tool life. It’s important to determine the maximum feed rate that maintains quality standards.
Depth of Cut
The depth of cut refers to the thickness of the material being removed in a single pass. Deeper cuts can improve efficiency but require more power and can increase tool wear. Striking a balance is essential for maintaining productivity without damaging the tool.
Advanced Coating Technologies for Enhanced Tool Life
Modern end mills utilize advanced coating technologies to improve performance and extend tool life. Understanding these coatings can help manufacturers select the right tools for their specific needs.
Popular Coating Types
1. **Titanium Nitride (TiN):** Provides a hard surface that enhances wear resistance and reduces friction, increasing tool life.
2. **Titanium Aluminum Nitride (TiAlN):** Suitable for high-temperature applications, TiAlN coatings improve hardness and oxidation resistance, making them ideal for mould steel processing.
3. **Diamond Coatings:** Ideal for non-ferrous materials, diamond coatings reduce wear and increase tool life significantly, although they are more expensive.
Benefits of Advanced Coatings
- **Increased Tool Life:** Coatings protect against wear and chip adhesion, resulting in longer-lasting tools.
- **Reduced Friction:** Lower friction during cutting can lead to better surface finishes and less heat generation.
- **Improved Chip Removal:** Enhanced coatings can help in effective chip evacuation, reducing the risk of re-cutting and tool damage.
Current Trends in End Milling Techniques
As technology evolves, new trends in end milling techniques are emerging, offering opportunities for increased efficiency and productivity in mould steel processing.
5-Axis Machining
5-axis machining allows for complex part geometries and reduces setup time by enabling multiple sides of a workpiece to be machined in one setup. This technique enhances precision and can significantly reduce cycle times.
Smart Tooling and Industry 4.0
The integration of smart tooling and sensors into end milling processes enables real-time monitoring of tool performance and machining conditions. This data-driven approach allows for predictive maintenance and process optimization, enhancing overall productivity.
Adaptive Machining
Adaptive machining techniques adjust cutting parameters in real-time based on feedback from the machining process. This flexibility can improve efficiency and tool life, reducing waste and downtime.
Measuring Productivity Gains with End Mill Solutions
To evaluate the effectiveness of end mill solutions in mould steel processing, manufacturers must establish key performance indicators (KPIs) that reflect productivity gains.
Key Performance Indicators
- **Tool Life:** Measure the duration a tool can operate before requiring replacement or sharpening.
- **Cycle Time:** Monitor the total time taken for each machining operation, including setup, cutting, and finishing.
- **Surface Finish Quality:** Evaluate the surface finish of machined parts to ensure they meet quality standards.
Continuous Improvement Strategies
Implementing continuous improvement strategies, such as Lean manufacturing and Six Sigma, can help organizations identify inefficiencies, optimize processes, and enhance productivity through better end mill solutions.
Frequently Asked Questions
1. What is the best material for end mills used in mould steel processing?
Carbide end mills are often the most suitable choice due to their hardness and wear resistance, making them ideal for machining tough mould steels.
2. How can I extend the life of my end mills?
Using appropriate cutting parameters, maintaining proper coolant flow, and selecting the right coatings can significantly extend the life of end mills.
3. What is the impact of tool geometry on machining performance?
The geometry of an end mill influences cutting forces, chip removal, and surface finish, making it crucial for achieving optimal machining outcomes.
4. How do I choose the right cutting speed for my application?
Cutting speed should be selected based on the material being machined, the type of end mill used, and the desired surface finish, often requiring trial and error to pinpoint the optimal value.
5. What role does coating play in end mill performance?
Coating enhances an end mill's wear resistance, reduces friction, and improves overall performance, allowing for higher speeds and feeds.
Conclusion: The Future of End Mill Solutions in Mould Steel Processing
As the manufacturing landscape continues to evolve, the importance of selecting the right end mill solutions for mould steel processing cannot be overstated. By understanding the various types of end mills, optimizing cutting parameters, leveraging advanced coating technologies, and staying abreast of emerging trends, manufacturers can significantly enhance productivity and maintain a competitive edge. The future of mould steel processing lies in innovation, and investing in advanced end mill solutions is a crucial step toward achieving operational excellence.
keywords
Latest News
Contact Information
Tel: +86-18861298766
E-mail: jeni@vellfire-tools.com
Whatsapp:8618861298766
Address: No. 156, Nanxi Road, Xinbei District, Changzhou City (Wilfa Recutting Milling Cutter and High Efficiency Drill Wholesale)

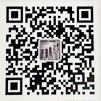

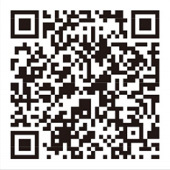
Copyright© 2023 Jiangsu Vellfire Precision Alloy Co., Ltd. All Rights Reserved
Business license