News
Titanium alloy milling cutter processing matters needing attention
Release time:
2022/12/29
titanium alloy milling cutterMany process parameters of forging, volume stamping and plate stamping are close to those of steel processing. However, there are several important characteristics that need to be paid attention to when stamping titanium alloy milling cutters. So, here we come to understand the titanium alloy milling cutter processing matters needing attention.
Although it is generally believed that the hexagonal lattice contained in titanium alloys is less plastic when deformed, various stamping methods used for other structural metals are also applicable to titanium alloys. The ratio of yield point to strength limit is one of the characteristic indicators of whether a metal can withstand plastic deformation. The greater this ratio, the worse the plasticity of the metal. In commercial pure titanium in the cold state, the ratio is 0.72-0.87. Carbon steel is 0.6-0.65. Stainless steel is 0.4-0.5.
Volume stamping, free features and other operations related to the processing of large cross-sections and large-size blanks are performed in the heated state (= μS above the transition temperature). Calcination and stamping heating temperatures range between 850-1150C. The alloys BT;M0, BT1-0, OT4 ~ 0 and OT4-1 have good plastic deformation in the cooled state. Therefore, parts made of these alloys are mostly stamped from intermediate annealed blanks without heating. Titanium alloy milling cutter in the cold plastic deformation, regardless of the chemical composition or mechanical properties, the strength will be a greater extent to raise the sideburns, the corresponding decline in plasticity, so the need for inter-process annealing.
titanium alloy milling cutterThe edge groove wear that occurs during machining is the wear of the rear and front parts along the cutting depth direction, and is mostly caused by the hardened layer remaining in the pretreatment. Chemical reaction and diffusion with the tool material whose processing temperature exceeds the 800 is also one of the reasons for the wear that forms the groove. This is because during the processing, the titanium molecules of the workpiece will accumulate in front of the blade and "weld" on the blade under high pressure and high temperature, forming debris accumulation. When the chip tumor is peeled off from the blade, it takes away the carbide coating of the blade.
Due to the heat resistance of titanium, cooling is very important in processing. The purpose of cooling is to prevent the blade and tool surface from overheating. By using an end cooling medium, a good chip removal effect can be obtained when machining pits, cavities or entire grooves of a chip mill or end mill. When the titanium alloy milling cutter is cutting titanium metal, the chip is easy to stick to the blade. If the next tool rotates to cut the chip again, the blade will often break. In order to solve this problem and enhance certain blade performance, each blade cavity has its own coolant hole/injection. Another ingenious solution is a threaded cooling hole. Long-bladed cutters have many blades. High pump capacity and pressure are required to pour coolant over each hole. On the other hand, if necessary, the unnecessary holes can be blocked, and the flow to the necessary holes can be increased to a large extent.
The above introduction istitanium alloy milling cutterProcessing considerations. If you need to know more, you can contact us at any time! Our company has many years of experience and looks forward to your joining at any time.
keywords
Previous Page
Previous Page:
Latest News
Contact Information
Tel: +86-18861298766
E-mail: jeni@vellfire-tools.com
Whatsapp:8618861298766
Address: No. 156, Nanxi Road, Xinbei District, Changzhou City (Wilfa Recutting Milling Cutter and High Efficiency Drill Wholesale)

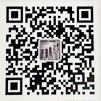

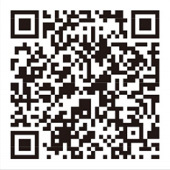
Copyright© 2023 Jiangsu Vellfire Precision Alloy Co., Ltd. All Rights Reserved